|
 |
CURING PROCESS FOR WEATHER STRIP (EXAMPLE BY “A” COMPANY)
1.Why this method has been selected
1) |
In continuous curing process of Weatherstrip by the previous line, its production speed was slow due to its no good thermal efficiency. |
2) |
In curing process of rubber, slow temperature raise for the Works caused inferior quality due to “Netsu-dare” (deformation such as distortion & flattening of rubber) |
3) |
Hourly running cost was high due to high gas consumption by this line |
2.Example of introduction of this method into new line
1)Previous line
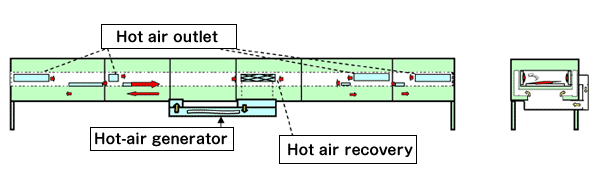
2)New line 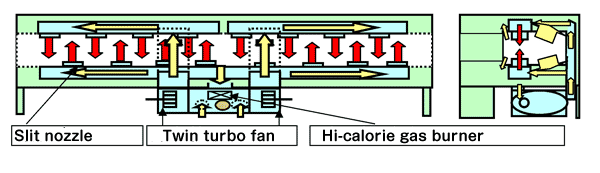
3.Result
1) |
Usage of Slit Nozzle has brought good thermal efficiency in which the Works are given uniform hot air so leading to high speed running of the new line. |
2) |
Impinging high temperature hot air to the Works at high speed has brought quick formation of skin layer so resulting in no more occurrence of “Nestsu-dare” as stated in above Item 1. |
3) |
Due to improvement of thermal efficiency, shortening of the line length has become possible so leading to efficient use of the space. |
4) |
Efficient hot air circulation has lessened hourly energy consumption so resulting in effective saving of the running cost by the new line. |
CURING OF CURVED HOSE (EXAMPLE BY “A” COMPANY
1.Why this method has been selected
? |
Batch type curing oven was used for secondary curing process of acrylic rubber hose and Steam pressure curing tube was used for rubber hose of thin thickness. |
? |
Production capacity was not stable and different depending on the skillfulness of the workers. |
2.Example of introduction of this method into new line
1)New line (continuous curing)
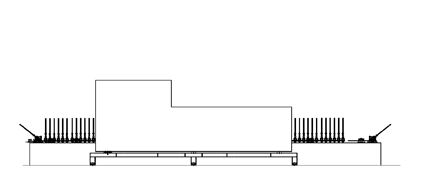
3.Result
1) |
Stable productivity has been realized by new continuous curing process |
2) |
At their batch type oven, thermal efficiency has been remarkably improved
by changing electric to gas use. |
3) |
At their pressure curing tube, water drainage was necessary caused by steam. It has become, however, no more necessary by the new system. |
|